
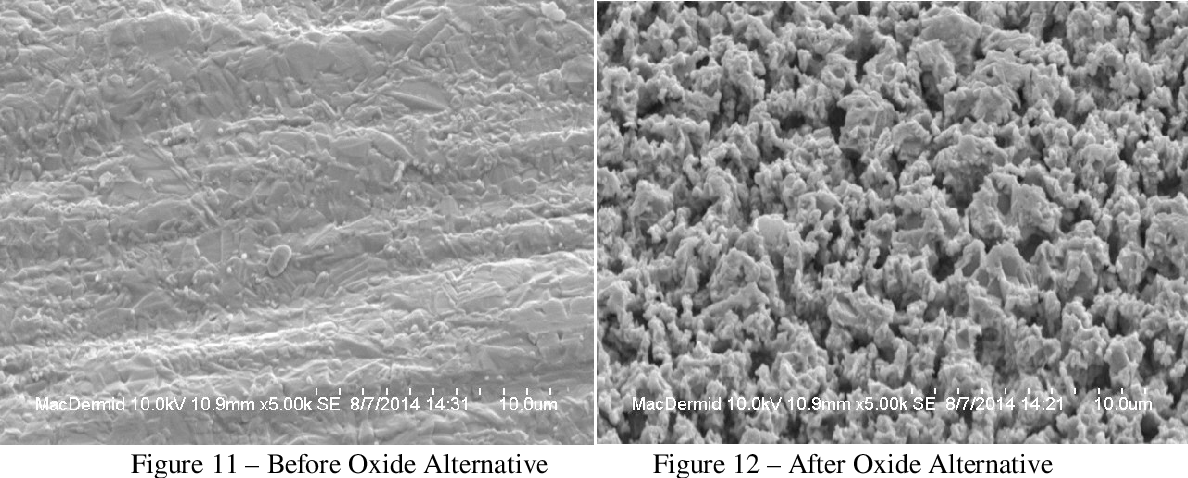
If I do all that on G-Wizard, the result is: 1834 rpm 12 ipm for a 0.100″ DOC and 1.8″ cut width. If your fly cutter has a lead angle, the ones pictured both do–the edge is angled, try using the lead angle feature on the Facemill type.
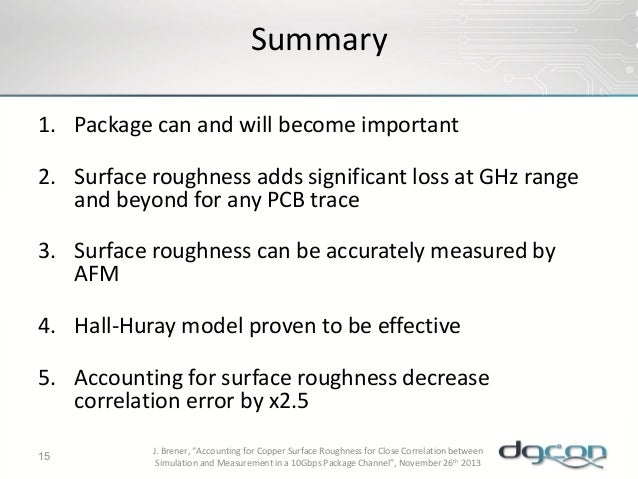
That’s exactly right–fly cutters are just face mills with only 1 cutting edge. The writer that prompted me to write this post had the right idea–just tell G-Wizard you’ve got a Face mill with only 1 insert. Now let’s get back to feeds and speeds: How do we set up G-Wizard for a fly cutter? To learn more about the non-feeds and speeds aspects of fly cutters, please visit our Fly Cutters page. Many say their secret weapon for fine aluminum finishing is a fly cutter with a PCD (diamond) insert. The exception are those most expensive face mills where you can individually adjust the cutting height of each insert to 0.0001″, because that’s what it takes, and that’s why fly cutters can leave a better finish. Remove all but one insert from your face mill, and finish improves. While the CNC crowd will more often prefer face mills, even many CNC machinists realize that the very best surface finish often comes from fly cutting.
#Roughness of flycut copper manual
I get asked about Fly Cutters a lot, there is a lot of traffic to my site on those keywords, and Fly Cutters are very commonly used by manual machinists. Let’s talk Fly Cutter Feeds and Speeds as long as we’re talking G-Wizard for manual machinists. With face mills that can’t be adjusted for height so they all match, each insert cuts a different chip load and this is what results in imperfections in the surface finish. The alternative is a face mill whose individual inserts can each be adjusted for height to eliminate the runout. You often hear fly cutters can give the best possible finishes (albeit at slower speeds), but why? If you remove all but one cutter from a face mill this converts the face mill to a fly cutter which has no runout. Running a cutter with a larger diameter helps speed that operation considerably.įly cutters Can Give Better Finish than Face Mills, But Why? Typically, you need to take just a little bit off a very large surface area. Here’s one more reason to use a fly cutter–it’s a great tool for surfacing your spoilboards on a CNC Router. Tormach’s Super Fly: Modern Riff on a classic machinist’s tool, the fly cutter… Here’s a good demo of a fly cutter from Tormach: OTOH, if you are going to finish the surface in some other way, perhaps not even on a milling machine, the fly cutter may be slower than a face mill at material removal rates.

In most cases, the best finish will be one that can be done in one pass, which implies a large diameter tool and therefore probably not a face mill. Many say their secret weapon for fine aluminum finishing is a fly cutter with a PCD (diamond) insert.ĬNC machinists realize the main reason to use a fly cutter is to achieve a very fine surface finish. While the CNC crowd will more often prefer face mills, even many CNC machinists realize that a very fine surface finish may be better done by fly cutting. I get asked about Fly Cutters and Fly Cutting a lot, there is a lot of traffic to CNCCookbook on those keywords, and Fly Cutters are very commonly used by manual machinists.
